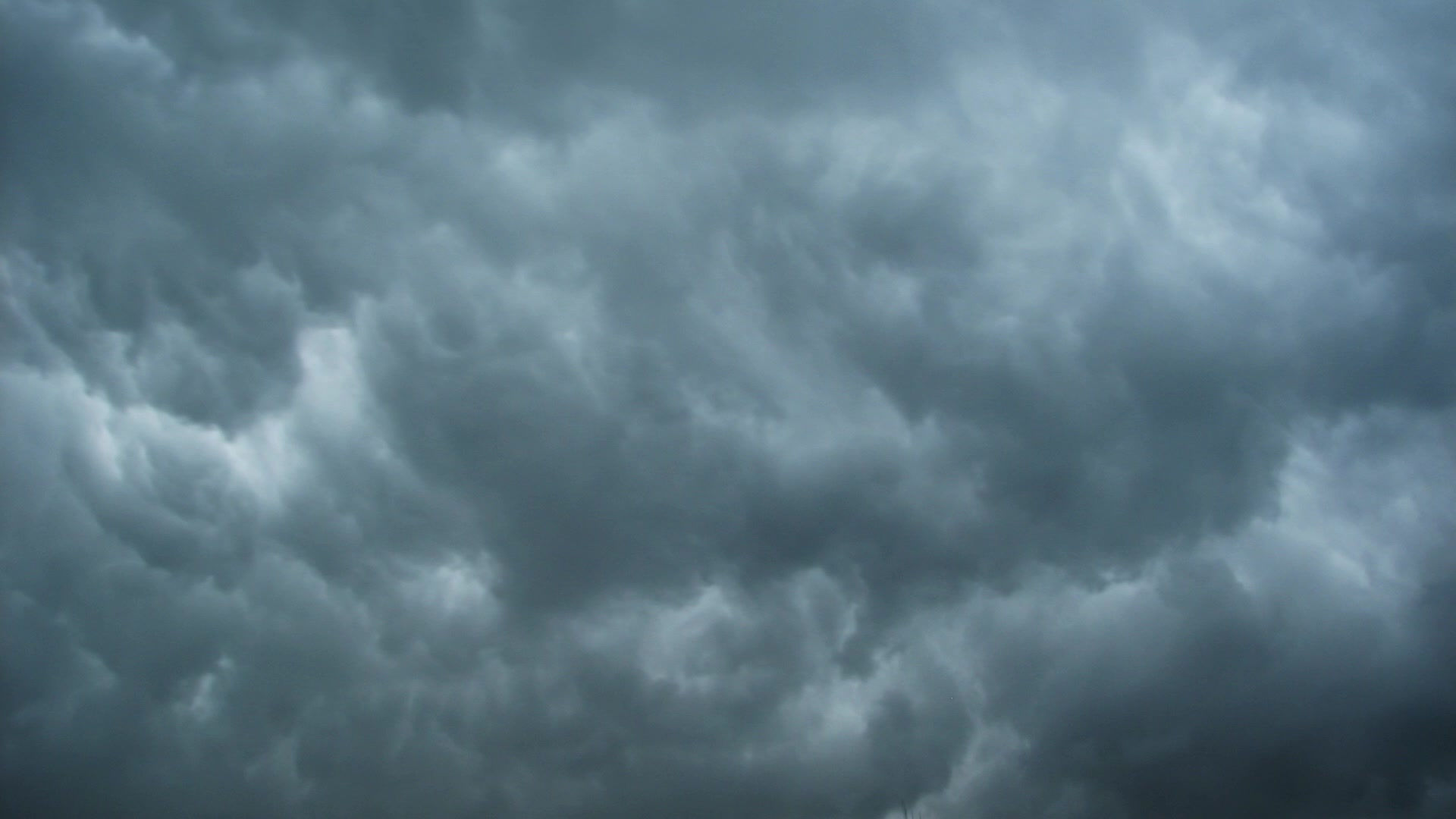

What you need to know
Each year there a number of serious fires on construction sites and buildings undergoing refurbishment.
Risk assessment
In most cases, conducting a risk assessment will be a relatively straightforward and simple task that may be carried out by the responsible person, or a person they nominate, such as a consultant.
There are five steps in carrying out a fire risk assessment:
1. Identify hazards: consider how a fire could start and what could burn;
2. People at risk: employees, contractors, visitors and anyone who is vulnerable, eg disabled;
3. Evaluation and action: consider the hazards and people identified in 1 and 2 and act to remove and reduce risk to protect people and premises;
4. Record, plan and train: keep a record of the risks and action taken. Make a clear plan for fire safety and ensure that people understand what they need to do in the event of a fire; and
5. Review: your assessment regularly and check it takes account of any changes on site.
Means of escape
Key aspects to providing safe means of escape on construction sites include:
· Routes: your risk assessment should determine the escape routes required, which must be kept available and unobstructed;
· Alternatives:well-separated alternative ways to ground level should be provided where possible;
· Protection: routes can be protected by installing permanent fire separation and fire doors as soon as possible;
· Assembly: make sure escape routes give access to a safe place where people can assemble and be accounted for. On a small site the pavement outside may be adequate; and
· Signs: will be needed if people are not familiar with the escape routes. Lighting should be provided for enclosed escape routes and emergency lighting may be required.
Means of giving warning
Set up a system to alert people on site. This may be temporary or permanent mains operated fire alarm (tested regularly), a klaxon, an air horn or a whistle, depending on the size and complexity of the site.
The warning needs to be distinctive, audible above other noise and recognisable by everyone.
Means of fighting fire
Fire extinguishers should be located at identified fire points around the site. The extinguishers should be appropriate to the nature of the potential fire:
· wood, paper and cloth – water extinguisher;
· flammable liquids – dry powder or foam extinguisher;
· electrical – carbon dioxide (C02) extinguisher.
Ways to prevent injuries and improve safety include:
1. Management safety
2. Integrate safety as a part of the job
3. Create accountability at all levels
4. Take safety into account during the project planning process
5. Make sure the contractors are pre-qualified for safety
6. Make sure the workers are properly trained in appropriate areas
7. Have a fall protection system
8. Prevent and address substance abuse to employees
9. Make safety a part of everyday conversation
10. Review accidents and near misses, as well as regular inspections
"Asbestos" is a commercial name, not a mineralogical definition, given to a variety of six naturally occurring fibrous minerals. These minerals possess high tensile strength, flexibility, resistance to chemical and thermal degradation, and electrical resistance. These minerals have been used for decades in thousands of commercial products, such as insulation and fireproofing materials, automotive brakes and textile products, and cement and wallboard materials.
When handled, asbestos can separate into microscopic-size particles that remain in the air and are easily inhaled. Persons occupationally exposed to asbestos have developed several types of life-threatening diseases, including asbestosis, lung cancer and mesothelioma. Although the use of asbestos and asbestos products has dramatically decreased in recent years, they are still found in many residential and commercial settings and continue to pose a health risk to workers and others.
First aid First aid can save lives, reduce pain and help an injured person make a quicker recovery. The Health and Safety (First Aid) Regulations 19816 require you to provide adequate and appropriate equipment, facilities and personnel to enable first aid to be given to your employees if they are injured or become ill at work. The minimum provision for all sites is:
â– a first aid box with enough equipment to cope with the number of workers on site; â– an appointed person to take charge of first-aid arrangements;
â– information telling workers the name of the appointed person or first aider and where to find them. A notice in the site hut is a good way of doing this. An appointed person is someone you choose to take charge when someone is injured or falls ill and who will telephone for an ambulance if one is required. An appointed person should not attempt to give first aid for which they have not been trained.
A first aider is someone who has undergone a training course in administering first aid at work and holds a current first aid at work certificate. A first aider can undertake the duties of an appointed person. The number of qualified first aiders needed depends on the risk of injury and ill health on site. As a guide: The first-aid arrangements should cover shift working, night and weekend working where this is carried out. This may mean appointing or training several people to ensure adequate cover.
Reporting injuries, diseases and dangerous occurrences Employers have a duty under the law (Reporting of Injuries, Diseases and Dangerous Occurrences Regulations 1995)7 to report to HSE certain types of accidents that happen to their employees. Whoever is in control of the site also has a legal obligation to report certain accidents which involve a self-employed worker or member of the public and certain dangerous occurrences. Generally, you have to report deaths, serious injuries and dangerous occurrences immediately and less serious injuries within ten days. Certain occupational ill-health issues and diseases also have to be reported. Further details of when you must report an accident, disease or dangerous occurrence are given in paragraphs 668-673.
Precautions to prevent fires
The following precautions should be taken to prevent fires:
â– use less-easily ignited and fewer flammable materials, eg use water-based or low-solvent adhesives and paint;
â– keep the quantity of flammables at the workplace to a minimum;
â– always keep and carry flammable liquids in suitable closed containers;
â– if work involving the use of flammable materials is being carried out, stop people smoking and don’t allow other work activities involving potential ignition sources to take place nearby. For example, if floor coverings are being laid using solvent-based adhesives, don’t allow soldering of pipes at the same time;
â– ensure that pipes, barrels, tanks etc which may have contained flammable gases or liquids are purged or otherwise made safe before using hot cutting equipment, such as a cutting torch or angle grinder. A pipe or container may appear to be empty, but can contain enough material on its sides, or within rust or other sediments, to produce a flammable or explosive atmosphere within it when heated or disturbed. Specialist advice may be required;
â– to minimise the risk of gas leaks and fires involving gas-fired plant: – close valves on gas cylinders when not in use; – regularly check hoses for wear and leaks; – prevent oil or grease coming into contact with oxygen cylinder valves; – do not leave bitumen boilers unattended when alight;
â– store flammable solids, liquids and gases safely. Separate them from each other and from oxygen cylinders or oxidising materials. Keep them in ventilated secure stores or an outdoor storage area. Do not store them in or under occupied work areas or where they could obstruct or endanger escape routes;
â– have an extinguisher to hand when doing hot work such as welding or using a disc cutter that produces sparks;
â– check the site at lunch time and at the end of the day to see that all plant and equipment that could cause a fire is turned off. Stop hot working an hour before people go home, as this will allow more time for smouldering fires to be identified; and
â– provide closed metal containers to collect rubbish and remove them from the site regularly. Collect highly flammable waste such as solvent-soaked rags separately in closed fire-resisting containers.
Work at height
To prevent or minimise risk when planning for work at height, consider the work to be done and take a sensible risk-based approach to identify suitable precautions. There is a hierarchy of control measures for determining how to work at height safely. The hierarchy has to be followed systematically and only when one level is not reasonably practicable may the next level be considered. Where it is reasonably practicable to prevent a fall, precautions should be taken to do so. It is not acceptable to select work equipment from lower down the hierarchy (eg personal fall arrest systems such as harnesses and lanyards) in the first instance.Those in control of the work must:
â– avoid work at height where they can .
â– use work equipment to prevent falls where work at height cannot be avoided;
â– where the risk of a fall cannot be eliminated, use work equipment to minimise the distance and consequences of a fall should one occur;
â– always consider measures that protect all those at risk, ie collective protection measures (scaffolds, nets, soft landing systems) before measures that only protect the individual, ie personal protection measures (a harness);
â– ensure work is carried out only when weather conditions do not jeopardise the health and safety of the workers. The hierarchy of control measures with practical examples:
â– Avoid working at height unless it is essential (eg erect guard rails on steelwork at ground level and then crane the steel and the guard rails into position; provide cast in mesh across riser ducts at the position of services; fix nets using extending poles).
â– Prevent falls by using an existing safe place of work that does not require the use or addition of work equipment to prevent a fall (eg a flat roof with permanent edge protection).
â– Prevent falls by using work equipment that protects all those at risk (eg access equipment fitted with guard rails, such as independent scaffolds, tower scaffolds, mobile elevating work platforms (MEWPs) and mast climbing work platforms (MCWPs)).
â– Prevent falls by using work equipment that protects the individual (eg a harness with a short lanyard which makes it impossible for a person to get to a fall position (this is called work restraint) or use a podium).
â– Mitigate falls by using work equipment to minimise the distance and consequences of a fall and protect all those at risk (eg nets or soft landing systems positioned close under the work surface).
â– Mitigate falls by using work equipment to minimise the distance and consequences of a fall and protect the individual (eg a personal fall arrest system with the anchorage point sited above the head, or a rope access system).
â– Mitigate falls by using work equipment that minimises the consequences of a fall (eg nets rigged at a lower level, or inflatable injury protection).
â– Mitigate falls through training, instruction or other means (eg ensure ladders are inspected regularly and are used by competent people, demarcate areas to provide a warning, provide adequate lighting, apply sensible housekeeping measures, provide suitable footwear etc).
Safe working platforms
A working platform is virtually any surface from which work is carried out, such as a roof, scaffold, MEWP, tower scaffold, trestle etc. It becomes a safe working platform when you can’t fall off it or through it or when measures have been taken to mitigate a fall from it. Make sure the working platform is:
â– capable of supporting the weight of the workers using it and any materials and equipment they are likely to use or store on it;
â– stable and will not overturn. For example, scaffolds usually need to be tied to a supporting structure and MEWPs should not be operated on sloping or uneven ground;
â– wide enough to allow people to pass back and forth safely and use any equipment or material necessary for their work at that place;
â– kept clear of loose materials and constructed to prevent materials from falling. As well as toe boards or similar protection at the edge of the platform, the platform itself should be constructed to prevent any object that may be used on the platform from falling through gaps or holes, causing injury to people working below. For scaffolds, a close-boarded platform would suffice, although for work over public areas, a double-boarded platform sandwiching a polythene sheet, fans or protected walkways may also be needed. If MEWPs or cradles are used and they have meshed platform floors, the mesh should be fine enough to prevent materials, especially nails and bolts, from slipping through;
â– free of openings and traps through which people’s feet could pass, causing them to trip, fall or be injured in any other way; and
â– kept free of tripping and slipping hazards. Keep platforms clean and tidy and do not allow materials or waste to build up on them.
General access scaffolds
Suitable precautions must be taken to prevent falls. General access scaffolds provide a means of working at height while preventing falls and should be provided whenever practicable. Scaffolds should be designed, erected, altered and dismantled only by competent people and the work should always be carried out under the direction of a competent supervisor. Scaffolders should always adopt methods of work to prevent falls during the erection of scaffolding. This can be achieved by using an advanced guard rail system. Where this is not practicable, harnesses should be worn to provide a means of fall arrest. For further information on erecting scaffolding, see the National Access and Scaffolding Confederation’s guidance note Preventing falls in scaffolding and falsework. Scaffolds should never be erected or dismantled over people or busy pavements. If the work presents a danger to the public, you should apply for a road closure to eliminate the risk of a member of the public being injured. If this is not granted, erection and dismantling should be done inside a segregated area and during the times when there are fewer members of the public in the vicinity. Ensure the scaffold is based on a firm, level foundation. The ground or foundation should be capable of supporting the weight of the scaffold and any loads likely to be placed on it. Watch out for voids such as basements or drains, or patches of soft ground, which could collapse when loaded. Provide extra support as necessary. Ensure it is braced and tied into a permanent structure or otherwise stabilised. Rakers only provide stability when they are braced and footed adequately; singletube rakers alone do not usually provide this and need to be braced to prevent buckling. Put ties in place as the scaffold is erected and only remove them in stages as it is struck. If a tie is removed to allow work to proceed, an equivalent tie should be provided nearby to maintain stability. Ties must be used within their safe working load limit. Proprietary system scaffods should be erected and tied according to the manufacturers’ instructions.
Before using any scaffold, make sure that it is safe and suitable for the intended job:
â– ensure platforms are fully boarded and wide enough for the work and for access (usually at least 600 mm wide);
â– check that scaffold boards are properly supported and not overhanging excessively (eg no more than four times the thickness of the board);
â– ensure there is safe access onto the work platforms, preferably from a staircase or ladder tower;
â– check that loading bays are fitted with fall protection, preferably gates, which can be safely moved in and out of position to place materials on the platform; and
â– make sure the scaffold is suitable for the task before it is used and checked whenever it is substantially altered or adversely affected, eg high winds.
Guard rails, toe boards and brick guards 148 Guard rails, toe boards and other similar barriers should be provided to prevent falls whenever practicable (see Figure 10). 149 They should:
â– be strong and rigid enough to prevent people from falling and be able to withstand other loads likely to be placed on them. For example, guard rails fitted with brick guards need to be capable of supporting the weight of stacks of bricks which could fall against them;
â– be fixed to a structure or part of a structure capable of supporting them;
â– include: – a main guard rail at least 950 mm above any edge from which people are liable to fall; – a toe board and brick guards where there is a risk of objects rolling or being kicked off the edge of the platform; and – a sufficient number of intermediate guard rails or suitable alternatives positioned so that the unprotected gap does not exceed 470 mm.
If a tower scaffold is used:
â– make sure it is resting on firm level ground with the locked castors or base plates properly supported – never use bricks or building blocks to take the weight of any part of the tower;
â– install stabilisers or outriggers when advised to do so in the instruction manual;
â– provide a safe way to get to and from the work platform, eg using an appropriately designed internal ladder;
â– provide edge protection (guard rails and toe boards) on all working platforms and platforms used for storing materials.
When erecting tower scaffolds:
â– do not exceed the safe height-to-base ratio in the instruction manual. Towers should never be erected to a height not recommended by the manufacturer;
â– do not use the working platform as a support for ladders, trestles or other access equipment;
â– do not overload the working platform;
â– do not fix ties to the centres of thin-walled aluminium tubes;
â– do not climb up the rungs on the end frames of the tower to reach the platform unless the rungs have been specifically designed for the purpose of getting to and from the working platform – these have rung spacings of between 230 and 300 mm and an anti-slip surface. When moving a mobile tower:
â– reduce the height to a maximum of 4 m;
â– check that there are no power lines or overhead obstructions in the way;
â– check that the ground is firm, level and free from potholes;
â– never move it while there are people or materials on the tower. When towers are used in public places, extra precautions are required:
â– erect barriers at ground level to prevent people from walking into the tower or work area;
â– minimise the storage of materials and equipment on the working platform;
â– remove or board over access ladders to prevent unauthorised access if they are to remain in position unattended. 166 To prevent the use of incorrectly erected or damaged tower scaffolds, they must be inspected regularly by a competent person. A new inspection and report is not required every time a tower scaffold is moved to a new location. However, if guard rails or other components have to be removed to enable the tower scaffold to be moved past an obstruction, then a pre-use check should be undertaken by a trained and competent user to make sure the tower has been reinstated correctly. In this situation, the use of a visible tag system (which can be updated each time a check is carried out) to supplement inspection records is one way of recording that the pre-use check has been undertaken.
When MCWPs are used, make sure:
â– a handover certificate is provided by the installer. The certificate should cover how to deal with emergencies, operate, check and maintain the equipment, and should state its safe working load;
â– there is a current report of thorough examination for the equipment;
â– masts are rigidly connected to the structures against which they are operating and outriggers are used when necessary;
â– working platforms are provided with suitable guard rails and toe boards;
â– the controls only operate from the working platform; and
â– the area below the platform is barriered off to prevent people from being struck by the platform or by objects that may fall from the platform.
When using cradles check that:
â– the cradle has adequate guard rails and toe boards and material cannot fall from or through the cradle’s base;
â– the equipment is capable of fitting closely to the building and where buffers or rollers are fitted, they will run against suitable features on the building;
â– the building is capable of carrying the loads placed upon it, particularly under the counterweights and under the fulcrum (or pivot point) of the outrigger. The advice of a structural engineer may be needed;
â– jib spacing matches the cradle length and, when the cradle can move, adequate stops are provided to prevent the cradle running off the end of the track;
â– jib length and counterweights are specified to give a factor of safety against overturning of no less than three;
â– a secondary safety rope fitted with a fall arrest device is provided and used;
â– adequate operating instructions and technical support are available. If the equipment is hired, the supplier should be able to advise;
â– the cradle is not overloaded and loads are placed on the platform as uniformly as possible;
â– there is safe access into the cradle. Access at ground level is safest. If access is from the roof, the cradle should be secured to prevent it swinging away from the building. Access must be possible without the need to climb up or down the suspension ropes. If access is from the roof, or other raised platform, suitable means to prevent falls from roof edges will be required (eg guard rails and toe boards); and
â– there is a plan for rescuing the operator if there is a cradle fault while at a high level.
On a ladder or stepladder:
â– do not overload it – the person and their equipment should not exceed the highest stated load;
â– do not overreach – keep your belt buckle inside the stiles and both feet on the same rung .Check the ladder is secure. Almost half of the accidents involving ladders happen because the ladder was not prevented from falling or slipping. The options for securing a ladder are as follows:
â– tie the ladder to a suitable point, making sure both stiles are tied ;
â– where this is not practicable, use an unsecured ladder supplemented with an effective ladder stability device (eg a ladder stay and anti-slip device). Such devices must ensure that the ladder does not run sideways, slide away from the wall or rotate about a stile;
â– securely wedge the bottom of the ladder to prevent it sliding, eg against a wall;
â– footing the ladder is the last resort and should be avoided by the use of other access equipment.
As a guide, when using ladders and stepladders:
â– check the stiles are not damaged, buckled or warped, no rungs are cracked or missing and the feet are in good repair and clean;
â– do not use home-made devices or equipment made for the DIY market, these are not strong enough for site work and should be avoided;
â– never try to repair damaged equipment;
â– ensure they are resting on a firm, level surface. Never place them on loose bricks or packing;
â– where a ladder is put up at an angle to minimise the risk of slipping outwards, as a rule of thumb the ladder needs to be ‘one out for every four up
â– make sure the top of the ladder rests against a solid surface. Ladders should not rest on fragile or other insecure surfaces such as cement sheet or plastic guttering (you may find a spreader bar or stand-off device useful);
â– ensure they are long enough: – for ladders, don’t use the top three rungs; – for stepladders, don’t use the top two steps unless a suitable handrail is available– don’t use the top three steps of a swing-back or double-sided stepladder where the step forms the very top of the stepladder
â– ensure the restraint devices on stepladders can be fully opened and any locking devices are engaged.
Occupational health risks Safety risks in construction have been recognised for some time. Occupational health risks have only recently started to be addressed. The main health risks in construction are:
â– musculoskeletal disorders: back and other muscle and joint injuries (see Moving, lifting and handling loads);
â– hand-arm vibration syndrome: pain and numbness in the fingers and hands caused by the use of vibrating tools .
â– dermatitis: redness and inflammation of the skin related to exposure to hazardous substances such as cements and solvents.
â– noise-induced hearing loss: deafness or ringing in the ears caused by exposure to high levels of noise;
â– asbestos-related diseases.
Assessment Look at the way people are exposed to the hazardous substance in the particular job that they are about to do. Decide whether it is likely to harm anyone’s health. Harm could be caused by:
â– Breathing in fumes, vapours, dust: does the manufacturer’s information say that there is a risk from inhaling the substance? Are large amounts of the substance being used? Is the work being done in a way that results in heavy air contamination, eg spray application? Is the work to be done in an area that is poorly ventilated, eg a basement? Does the work generate a hazard, eg hot cutting metal covered with lead causes lead fumes to be given off?
â– Direct contact with skin: does the manufacturer’s information say there is a risk from direct contact? How severe is it, eg are strong acids or alkalis being used? Does the method of work make skin contact likely, eg from splashes when pouring from one container to another, or from the method of application?
â– Swallowing or eating contaminated material: some materials can contaminate the skin and hands. The contamination can then be passed to a person’s mouth when they eat or smoke. This is a particular problem when handling lead and sanding lead-based paint. Make sure people do not smoke or eat without washing first.
Personal protective equipment If, and only if, exposure cannot be adequately controlled by any combination of the measures already mentioned, you will need to provide personal protective equipment (PPE). Any PPE must be selected with care. Choose good quality equipment which is CE-marked. Let the user of the equipment help choose it – they will be more willing to wear it. Explain to the user why the equipment has to be worn and the hazard(s) the equipment protects against. Respiratory protection Respirators can protect against dusts, vapours and gases. There are many types of respiratory protective equipment (RPE), including:
â– disposable face mask respirators;
â– half-mask dust respirators;
â– high-efficiency dust respirators;
â– positive-pressure powered respirators;
â– ventilator visor or helmet respirators;
â– compressed air line breathing apparatus;
â– self-contained breathing apparatus. Make sure the respirator is the correct type for the job; dust masks may not protect against vapours or vice versa. If the respirator has replaceable cartridges, make sure the correct type is fitted, that they have not become exhausted or clogged and are still in date (many filters have a limited shelf life). Have replacement filters available. A competent person should select RPE that is both suitable for the user and the job, as this choice will depend upon a number of factors, including:
â– the nature of the hazards and materials;
â– the measured level of the contaminant;
â– the period of exposure;
â– if working outdoors, the prevailing weather conditions;
â– suitability for each user, such as field of vision, provision for communication and the ease of movement in cramped working places, eg confined spaces.
It is essential that respirators fit well around the face. Make sure the user knows how to wear the equipment and check for a good face seal. Respirators do not seal well against a beard, so when the user has a beard, alternative protection is needed, such as air-fed visors, which do not rely on a good face seal. Users need to know how the respirator should be fitted and operated and what maintenance checks they should carry out. Supervise the user to make sure they are using the respirator properly and regularly checking it for damage. Make sure the respirator does not become a source of contamination by keeping it clean. Store it in a clean box or cupboard – don’t leave it lying around in the work area. Skin protection Dermatitis is an inflammatory skin condition caused by certain irritants contained in many industrial materials. There are two general types:
â– irritant dermatitis: usually caused by the skin coming into contact with an irritant substance. Anyone can be affected and the strength of the irritant together with the duration of exposure will affect the seriousness of the complaint;
â– sensitising dermatitis: where a person develops an allergic reaction to a substance. The reaction may follow weeks, months or even years of use without any ill effects but once it has occurred, any future exposure to the substance will produce an adverse reaction.
Reaction of the skin to an irritant varies from one individual to another. The reaction may be only a mild redness but this can develop into swelling, blisters and septic ulcers that are both unsightly and painful .In addition to dermatitis, some substances can cause other skin problems, such as oil acne from bitumen-based products and skin ulcers from corrosive substances.
In the course of their work, construction workers may come into contact with many skin irritants. The most common types include:
â– cement, lime and plaster;
â– paint;
â– tar, pitch and bitumen;
â– solvents, thinners and de-greasers;
â– certain epoxy, acrylic and formaldehyde resins;
â– mineral oils and grease. Where protective clothing is provided (such as overalls and gloves), it must be of the right type to protect the wearer against the particular hazard they are going to encounter. All manufacturers offer advice on the most suitable gloves for specific types of hazard. When using gloves to help prevent dermatitis, users must avoid getting contaminants inside the gloves when putting them on and taking them off. It is also essential to provide washing facilities, with a supply of hot and cold (or warm) running water, soap and a means of drying the hands, to help prevent dermatitis. Advice on general PPE is contained in paragraphs 530-546, and advice on measures to protect against noise and vibration can be found in the sections specific to those topics.
further advice may be obtained from:
â– the Construction Industry Training Board (CITB);
â– employers’ and trade organisations such as the Building Employers’ Confederation (BEC), the Federation of Master Builders (FMB) and the Construction Federation;
â– training and enterprise councils and local enterprise companies;
â– local health and safety groups;
â– insurance companies;
â– suppliers – they must provide instructions on using machines, tools, chemicals etc and product data sheets. Also, containers often have helpful labels;
â– safety magazines – they have useful articles and advertise safety products and services;
â– the British Safety Council (BSC), the Royal Society for the Prevention of Accidents (RoSPA), the Institution of Occupational Safety and Health (IOSH) and many other independent companies and consultants run training courses – look in the telephone directory;
â– HSC publishes a newsletter about new HSE publications, changes in the law and similar items of interest, and there is also a twice-yearly newsletter for the construction industry entitled Site Safe News;
â– the HSE website: www.hse.gov.uk/construction.
The key provisions of the Regulations are that duty holders should:
â– avoid work at height where they can;
â– use work equipment to prevent falls where work at height cannot be avoided;
â– where the risk of a fall cannot be eliminated, use work equipment to minimise the distance and consequences of a fall should one occur;
â– always use measures which afford protection to everyone at risk (eg nets) before using personal protective measures (eg harnesses);
â– ensure that the work is risk-assessment based and that the most suitable item of work equipment is selected and used;
â– ensure those involved in work at height, including its planning and organisation, are competent to the level required to carry out their duties safely;
â– inspect working platforms and work equipment at defined intervals and record the results (see Appendix 1);
â– control risks from work involving fragile surfaces.
What COSHH requires:
â– Step 1: Assess the risks to health arising from hazardous substances used or created by your workplace activities.
â– Step 2: Decide what precautions are needed. You must not carry out work which could expose your employees to hazardous substances without first considering the risks and the necessary precautions and what else you need to do to comply with COSHH.
â– Step 3: Prevent or adequately control exposure. You must prevent your employees being exposed to hazardous substances. Where preventing exposure is not reasonably practicable, then you must adequately control it.
â– Step 4: Ensure that control measures are used and maintained properly and that safety procedures are followed.
â– Step 5: Monitor the exposure of employees to hazardous substances if necessary.
â– Step 6: Carry out appropriate health surveillance where your assessment has shown this is necessary or where COSHH sets specific requirements.
â– Step 7: Prepare plans and procedures to deal with accidents, incidents and emergencies involving hazardous substances where necessary.
â– Step 8: Ensure employees are properly informed, trained and supervised.
Employees’ duties
Employees also have health and safety duties. They should:
â– follow instructions given to them by their supervisors;
â– co-operate with their employer on health and safety matters;
â– follow the health and safety rules that apply to their particular job and to the site in general;
â– use the health and safety equipment provided;
â– report defects in equipment to their supervisor;
â– take care of their own health and safety as well as that of their workmates and others who might be affected by their work. Employees should be trained to know what to do and the work should be supervised and monitored to make sure that information provided as training is relevant to the work situation and is applied effectively. Deciding whether somebody is an employee or is self-employed can be complex in the construction industry. It may be important to be sure of the employment status of people working on a site. It may affect who has responsibility for some aspects of health and safety and the provision of safety equipment such as boots and hats.
Employers must report accidents to their employees.
Whoever is in control of the site must also report accidents involving a self-employed worker or member of the public. Any of the following types of accident which happen on site have to be reported:
â– serious and fatal accidents must be notified without delay to HSE, normally by telephone;
â– this must be followed up with a completed accident report form (F2508) within ten days;
â– for less serious injuries, where the injured person is unfit (or unable) to do their normal job for more than three consecutive days, a completed accident report form F2508 must be sent to HSE within ten days;
â– if a dangerous occurrence happens on site, eg a building, scaffold or falsework collapse, failure of a crane or lifting device or contact with overhead lines, it must be reported immediately, normally by telephone, to the nearest HSE office. The details must be confirmed within ten days on a completed accident report form (F2508);
â– if a worker suffers from a specified disease associated with their current job, eg hand-arm vibration syndrome and some forms of dermatitis, it must be reported to HSE on a completed disease report form (F2508A). The forms referred to are available at www.hse.gov.uk, or from your local HSE office.
A record must be kept of any reportable injury, disease or dangerous occurrence. This must include the date and method of reporting, the date, time and place of the event, personal details of those involved and a brief description of the nature of the event or disease. The record can be kept in any form preferred, eg keep copies of completed report forms in a file.
Inspectors and the law Health and safety laws that apply to construction companies are usually enforced by an inspector from HSE. However, some smaller jobs inside offices, shops and similar premises are the responsibility of inspectors from the local authority. One of the jobs of health and safety inspectors is to see how well site hazards are being dealt with, especially the more serious ones that could lead to injuries or ill health. They may wish to investigate an accident or a complaint. Inspectors do visit workplaces without notice but everyone is entitled to see their identification before letting them look around. Don’t forget that they are there to give help and advice, particularly to smaller firms that may not have a lot of knowledge. When they do find problems they will try to deal with the firm in a reasonable and fair way. If anyone is not satisfied with the way they have been treated, they can take the matter up with the inspector’s manager, whose name is on all letters from HSE. Any complaint about HSE inspectors will be investigated, and firms will be told what is to be done to put things right if a fault is found. Inspectors do have wide powers, which include the right of entry to premises, the right to talk to employees and safety representatives and to take photographs and samples. They are entitled to workers’ co-operation and answers to questions. They have the right to take written statements from anyone who can help them with their investigation. If there is a problem, they have the right to issue a notice requiring improvements to be made or (where a risk of serious personal injury exists) one which stops a process or the use of dangerous equipment. If a business receives an improvement or prohibition notice, it has the right to appeal to an industrial tribunal. If the business appeals against an improvement notice, the action required by the notice is suspended until the appeal is finished. The action required by a prohibition notice is not suspended pending an appeal because that could allow a serious risk to persist. Inspectors do have the power to prosecute a business or an individual for breaking health and safety law, but they will take their attitude and safety record into account.
Access on site
â– Can everyone get to their place of work safely?
â– Are access routes free from obstructions and clearly signposted?
â– Are holes protected with clearly marked and fixed covers to prevent falls?
â– Are temporary structures stable, adequately braced and not overloaded?
â– Will permanent structures remain stable during any refurbishment or demolition work?
â– Is the site tidy, and are materials stored safely?
â– Is lighting adequate, especially when work is being carried on after dark outside or inside buildings? Welfare
â– Are toilets readily available and are they kept clean and properly lit?
â– Are there washbasins, hot and cold (or warm) running water, soap and towels?
â– Are the washbasins large enough to wash up to the elbow and are they kept clean?
â– Is there somewhere to change, dry and store clothing?
â– Is there a place where workers can sit, make hot drinks and prepare food?
â– Are drinking water and cups provided?
â– Can everyone who needs to use them get to the welfare facilities easily and safely? Scaffolds
â– Are scaffolds erected, altered and dismantled by competent people?
â– Are all uprights provided with base plates (and where necessary, timber sole plates)?
â– Are all uprights, ledgers, transoms and braces in position?
â– Is the scaffold tied to the building or structure in enough places to prevent collapse?
â– Are there double guard rails and toe boards or other suitable protection at every edge, to prevent falling?
â– Are brick guards provided to prevent materials falling from scaffolds?
â– Are the working platforms fully boarded and are the boards arranged to avoid tipping or tripping?
â– Are there effective barriers or warning notices in place to stop people using an incomplete scaffold, eg where working platforms are not fully boarded?
â– Is the scaffold strong enough to carry the weight of materials stored on it and are these evenly distributed?
â– Does a competent person inspect the scaffold regularly, eg at least once a week if the working platform is 2 m or above in height or at suitable intervals if less than 2 m, and always after it has been altered or damaged and following extreme weather?
â– Are the results of inspections recorded and kept?
â– Have proprietary tower scaffolds been inspected and are they being used in accordance with suppliers’ instructions?
â– Have the wheels of tower scaffolds been locked and outriggers deployed when in use and are the platforms empty when they are moved? Ladders
â– Does your risk assessment conclude that ladders are the right way to the job? Don’t work from a ladder if there is a safer way using more suitable equipment!
â– Are the ladders in good condition?
â– Do ladders rest against a solid surface and not on fragile surfaces or insecure materials?
â– Are they secured to prevent them slipping sideways or outwards?
â– Do ladders rise a sufficient height above their landing place (about five rungs)? If not, are other handholds available?
â– Are the ladders positioned so that users do not have to overstretch? Roof work
â– Is there edge protection to stop people or materials falling?
â– During industrial roofing, have nets been provided to stop people falling from the leading edge of the roof and from partially fixed sheets?
â– Where nets are used, have they been rigged safely by a competent person?
â– Have you identified fragile surfaces such as fibre cement sheets and roof lights?
â– Have you taken precautions to stop people falling through fragile surfaces when working on the roof, eg by providing barriers, covers or working platforms?
â– Are people kept away from the area below the roof work? If this is not possible, have additional precautions been taken to stop debris falling onto them? Powered access equipment
â– Has the equipment been installed by a competent person?
â– Are the operators trained and competent?
â– Is the safe working load clearly marked?
â– Is the equipment inspected by a competent person?
â– Does the working platform of the powered access equipment have adequate, secure guard rails and toe boards or other barriers to prevent people and materials falling off?
â– Have precautions been taken to prevent people being struck by: – the moving platform; – projections from the building; or – falling materials?
Manual handling
â– Are there heavy materials such as roof trusses, concrete lintels, kerbstones or bagged products which could cause problems if they have to be moved by hand? If so, can you: – choose lighter materials; – use wheelbarrows, hoists, telehandlers and other plant or equipment so that manual lifting of heavy objects is kept to a minimum; – order materials such as cement and aggregates in 25 kg bags; and/or – avoid the repetitive laying of heavy building blocks weighing more than 20 kg?
â– Have people been instructed and trained how to lift safely? Hazardous substances
â– Have you identified all harmful substances and materials, such as asbestos, lead, solvents, paints, cement and dust?
â– Have you checked whether a licensed contractor is needed to deal with asbestos on site? (Most work with asbestos requires a licence, although you can do some very limited work with material that contains asbestos without one.)
â– Have you identified and put into place precautions to prevent or control exposure to hazardous substances, by: – doing the work in a different way, to remove the risk entirely; – using a less hazardous material; or – using tools fitted with dust extraction?
â– Have workers had information and training so they know what the risks are from the hazardous substances used and produced on site, and what they need to do to avoid the risks?
â– Have you got procedures to prevent contact with wet cement (as this can cause both dermatitis and cement burns)?
â– Have you arranged health surveillance for people using certain hazardous substances (eg lead)?
Noise
â– Have workers had information and training so they know what the risks are from noise on site, and what they need to do to avoid those risks?
â– Have you identified and assessed workers’ exposure to noise?
â– Can the noise be reduced by using different working methods or selecting quieter plant, eg by fitting breakers and other plant or machinery with silencers?
â– Are people not involved in the work kept away from the source of the noise?
â– Is suitable hearing protection provided and worn in noisy areas?
â– Have hearing protection zones been marked?
â– Have you arranged health surveillance for people exposed to high levels of noise? Hand-arm vibration
â– Have workers had information and training so they know what the risks are from hand-arm vibration (HAV) on site, and what they need to do to avoid those risks?
â– Have you identified and assessed risks to workers from prolonged use of vibrating tools such as concrete breakers, angle grinders or hammer drills?
â– Has exposure to HAV been reduced as much as possible by selecting suitable work methods and plant?
â– Are reduced-vibration tools used whenever possible?
â– Have vibrating tools been properly maintained?
â– Have you arranged health surveillance for people exposed to high levels of hand-arm vibration, especially when exposed for long periods?
Electricity and other services
â– Have all necessary services been provided on site before work begins and have you also identified existing services present on site (eg electric cables or gas mains) and taken effective steps (if necessary) to prevent danger from them?
â– Are you using low voltage for tools and equipment, eg battery-operated tools or low-voltage systems?
â– Where mains voltage has to be used, are trip devices (eg residual current devices (RCDs)) provided for all equipment?
â– Are RCDs checked daily by users and properly maintained?
â– Are cables and leads protected from damage?
â– Are all connections to the system properly made and are suitable plugs used?
â– Are tools and equipment checked by users, visually examined on site and regularly inspected and tested by a competent person?
â– Where there are overhead lines, has the electricity supply been turned off, or have other precautions been taken, such as providing ‘goal posts’ or taped markers?
â– Have hidden electricity cables and other services been located (eg with a locator and plans) and marked, and have you taken precautions for safe working?
Tools and machinery
â– Are the right tools or machinery being used for the job?
â– Are all dangerous parts guarded, eg gears, chains drives, projecting engine shafts?
â– Are guards secured and in good repair?
â– Are tools and machinery maintained in good repair and are all safety devices operating correctly? â– Are all operators trained and competent?
Fires and emergencies
General
â– Are there emergency procedures, eg for evacuating the site in case of fire or for rescue from a confined space?
â– Do people on site know what the procedures are?
â– Is there a means of raising the alarm, and does it work?
â– Is there a way to contact the emergency services from site?
â– Are there adequate escape routes and are these kept clear?
â– Is there adequate first-aid provision?
Fire
â– Is the quantity of flammable materials, liquids and gases on site kept to a minimum?
â– Are they properly stored?
â– Are suitable containers used for flammable liquids?
â– Are flammable gas cylinders returned to a ventilated store at the end of the shift?
â– Are smoking and other ignition sources banned in areas where gases or flammable liquids are stored or used?
â– Are gas cylinders, associated hoses and equipment properly maintained and in good condition?
â– When gas cylinders are not in use, are the valves fully closed?
â– Is flammable and combustible waste removed regularly and stored in suitable bins or skips?
â– Are suitable fire extinguishers provided?
Gateway Qualifications: promoting learning, rewarding achievement. Your Awarding Organisation and Access Validating Agency. http://www.gatewayqualifications.org.uk/